Safety Program Development
Occupational Health and Safety (OHS) requires employers with 20 or more regularly employed workers to have a health and safety program. Employers with fewer than 20 regularly employed workers are not required to have a program but must have documentation in place that meets the requirements established by OHS legislation. Under OHS legislation, a health and safety program must, at minimum, contain elements such as hazard assessment, health and safety committees and worker training. When applying for a COR certification, there are several additional elements that must be included to meet the industry standard.
What is a Safety Manual?
A safety manual is fundamental to a safety program by providing a collection of information, instructions, policies, and procedures intended to ensure the safe operations of companies that perform hazardous work. An effective safety manual empowers all levels of employees within a company to foster a safe work environment. It educates supervisors and workers, providing them with the tools to help complete their jobs safely.
Why Does My Business Need A Safety Program?
It’s an employer’s obligation to ensure employee safety. Because it’s not possible to supervise employees at all times, it’s important to develop standards and formalize them as policies and procedures to be executed by the safety program. An effective safety program helps prevent fatalities, injuries, illnesses, property or equipment damage, and harm to the environment.
Who Benefits From a Safety Program?
All levels of leadership and employees benefit from a clear, concise and comprehensive safety manual.
- Management uses the safety program as an essential training tool, allowing them to communicate the intent and execution of health and safety policies and procedures to the company.
- Supervisors use the safety program to ensure the workers they are supervising are performing work as per the policies and procedures.
- Workers use the safety program to know how to execute work safely at the field level.
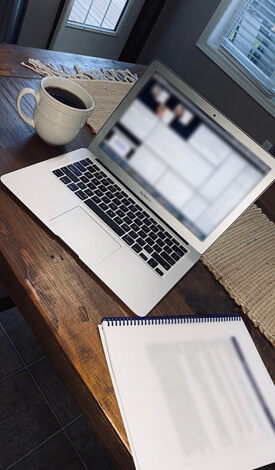
What is a Safety Manual?
A safety manual is fundamental to a safety program by providing a collection of information, instructions, policies, and procedures intended to ensure the safe operations of companies that perform hazardous work. An effective safety manual empowers all levels of employees within a company to foster a safe work environment. It educates supervisors and workers, providing them with the tools to help complete their jobs safely.
Why Does My Business Need A Safety Program?
It’s an employer’s obligation to ensure employee safety. Because it’s not possible to supervise employees at all times, it’s important to develop standards and formalize them as policies and procedures to be executed by the safety program. An effective safety program helps prevent fatalities, injuries, illnesses, property or equipment damage, and harm to the environment.
Who Benefits From a Safety Program?
All levels of leadership and employees benefit from a clear, concise and comprehensive safety manual.
- Management uses the safety program as an essential training tool, allowing them to communicate the intent and execution of health and safety policies and procedures to the company.
- Supervisors use the safety program to ensure the workers they are supervising are performing work as per the policies and procedures.
- Workers use the safety program to know how to execute work safely at the field level.
What Should Be In A Safety Manual?
When creating a safety manual, the principal goal is to provide policies regarding the operations of the company and the steps that employees are to take to perform their jobs safely and efficiently. The manual will cover some of the following items:
- Hazard and risk assessment
- Safe Work Practices and Safe Job Procedures
- Employee training
- Preventative maintenance
- Worksite inspection requirements
- Incident investigation
- Substance abuse
- Emergency Preparedness
- Personal Protective Equipment
- Workplace violence and harassment
- Health and safety committees
Why Digitalize A Safety Manual?
There are numerous advantages and efficiencies resulting from a digitalized safety manual.
- Reduced paperwork
- Zero risk of lost or compromised reports
- Instant access to safety documents (company policies, SDS, JSA, SWP, SJP etc.)
- Efficient compliance (faster response, more efficient actions)
- Timely alerts (upcoming deadlines, expirations, renewal dates, best-before dates)
- Real-time information and insights
- Incontrovertible evidence that hazards are corrected (time-stamped and location-stamped photos)
- Improved company culture (signals employees that their safety is of vital importance)
- Increased compliance
- Reduced costs (fewer accidents, reduced labour for managing documents)
- Boosted employee confidence (feel protected, know how to handle risk & report hazards)
- Improved company image
- Ease of audit (quickly collect sample documentation)
- Creation of custom forms (FLHA, Toolbox Talks, Inspections, Incident Investigations, JSA’s, Near Miss/HID Forms, etc.)
A health and safety program demonstrates to management, supervisors and workers that there is a commitment to ensuring high standards of health and safety. A safety manual covers how to keep all employees safe while participating in the company’s operations. Digitalizing your safety manual provides ease and speed of use and simplifies compliance with OHS and COR standards.
Need help developing a digital safety program? Want assistance digitalizing an existing program? Let 1st Quality Safety Consulting help you. Go digital with the help of Site App Pro, a digital safety management software that leaves your safety program paperless and always at your fingertips. Compatible with all iOS (Apple) and Android devices. For more information about how we can help you implement a Digital Safety Program, click the button below!